The most common materials used in desktop FDM 3D printing are PLA, ABS, HIPS and PVA on a spool in reel form. Other materials used by the industry are nylon, glass polyamis, stereolithography (poxy resin), wax, ceramics, photopolymers, polycarbonate and metals such as silver, titanium and steel.
Most materials can be found from different manufacturers and vendors at different prices. Furthermore the Quality and the Properties will vary from manufacturer to manufacturer. Finding a good filament is an essential part of the 3DP workflow. You will get what you have paid for. There are new materials hitting the market everyday and you will always be abel to find the right material for your project. This is an overview of the materials we have worked with and tested, but the market nowadays is not limited to only those !
Beginners Use
_
ABS
ABS is very durable, strong and slightly flexible material. It is suitable for a large variety of purposes. ABS is used in automotive components, electronics assemblies, music instruments, toys, protective cases, kitchen appliances, and is most famous as the material of Lego® toys. The material requires a heated bed and it can be easily post-processed after printing!
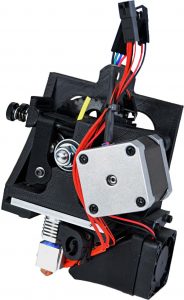
ABS 3D Printed Extruder
PROS:
- Excellent plastic properties
- Durable
- Excellent for mechanical parts
- Heat resistant
- Easy for post processing
CONS:
- Heated bed and/or chamber required
- Slightly smelly
- Toxic when melted
- Tends to warp and in tall objects a layer separation (cracks) can happen
PLA
PLA is currently the most environmentally friendly material used in desktop FDM 3D printing. It is made from renewable sources of plant starch. The material is used in food packaging, bags, disposable tableware, feminine hygiene products, and even in diapers. It doesn’t require a heated bed and is non-toxic. In addition, for beginners PLA is considered as the easiest material to print with and it’s available in almost any color. You can get a high definition prints, but they will not be as strong or as durable as ABS products. The filament is not good for prints that will be exposed to high heat. Moreover PLA can be used as a supportive material for ABS designs with a dual or printers with multiple extruders.
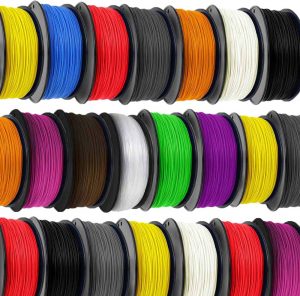
PLA Colors Variety
PROS:
- Bio-plastic
- Good smell
- Non-toxic
- No heated bed required
- High print speed
- Less wrapping and shrinking
- Excellent for small and tall high-resolution parts
- Hard or flexible variants
- Many colors available
- Easy to paint
CONS:
- Slow cooling down
- Low heat resistance
- Easier to break
- Limited post processing – sanding, gluing etc
HIPS
HIPS is used as alternative to ABS. Similarly, it is relatively strong, but more unlikely to warp and crack like ABS. Thus easier to print with. Also, the low cost makes it the best choice among all other materials used in desktop FDM 3d printing for rapid prototyping, early design testing and educational purposes. Furthermore HIPS 3D printing filaments are used as support material in printers with a dual or multiple extruders, in order to provide structure to object with complex geometry. HIPS is Limonene soluble and it’s ideal for support structures, for parts with a lot of overhangs, moving interlocking parts of great complexity and more…
PROS:
- Excellent plastic properties
- Durable
- Excellent for mechanical parts
- Heat resistant
- Easy post processing
- Wide range of colors
CONS:
- Heated bed required
- Slightly smelly
nGen
nGen is co-polyester filament specifically designed for Desktop FDM 3D printing. It has a superior melt strength and dimensional accuracy. This material offers good bridging capabilities. And it handles overhangs better than most filaments. Objects printed with nGen show sparkling clarity and gloss. The filament is great for complex functional prototypes and 3D printed productions. Still it’s easy to print with!
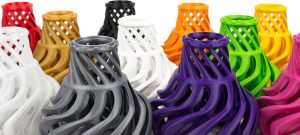
nGen 3D Printing Filament
PROS:
- Low odor
- Low emissions
- Suitable for small office space
- Styrene-free
CONS:
- Expensive compare to other filaments
- Fewer colors available
- Only one manufacturer
Intermediated Use
_
MAGNETIC IRON, STEEL, WOODFILL, COFFEE, COOPERFILL, BRONZEFILL – PLA
All those are PLA base filaments with add-on fibers or powders of other materials like wood, steel, magnetic iron etc. Their main purpose is surface finish. Those materials are great for arts, concept models and even for some consumer end-products. Moreover some high-end post processing techniques are suitable for those filaments like rusting, staining, polishing and the final results could be very impressive and misleading that is not plastic.
PROS:
- Great look and texture finish
- Variety of post-processing techniques
CONS:
- Not so durable & strong
- Require specific (abrasive resistant) hot end
T-glasse/PETT
T-glasse which is short for “Tough Glass”. It’s stiff and clear filament. The material is a highly translucent. It can reflect and transmit light and provides a great surface finish! T-glasse is the first 3D printing material to be approved by FDA as Food Safe and it’s 100% Recyclable.
PROS:
- Food safe (FDA Approved)
- 100% recyclable
- Low odor
CONS:
- Requires Special storage (absorbs water from the air)
- Prints slow
TPU – NinjaFlex & SemiFlex
This is a rubber like filament that that has wide range of applications. It’s highly flexible and has a soft feel. Different flex-properties can be achieved when varying the number of outlines – shells – parameters and the percentage of infill. TPU – NinjaFlex and SemiFlex are great for functional prototypes like phone cases, hinges, shoe soles, watch bands etc.
PROS:
- Extremely strong & durable
- Doesn’t require heated bed
CONS:
- Requires a 3D Printer upgrade (in most cases)
- Prints slow
Alloy 910 by Taulman
This is one of the strongest materials you can 3D print with! The tensile strength of 8,100+ PSI makes Alloy 910 as strong as Polycarbonate, but way easier to print with, because it warps 5 times less than PC! You can use Alloy 910 for height strength and stiff parts. Also, the material like all other nylon filaments has a wide range of chemical resistance!
Bridge Nylon by Taulman
Bridge combines the strength of nylon 645 with the price of ABS and PLA filaments. Offers a better adherence to the printing platform, reduced water up-take from local humidity and reduced shrinkage that makes it easy to print. Printed parts from that material are stronger and more resilient than 3D prints from common materials like ABS and PLA.
Expert Use
_
PVA
PVA in 3D printing is used as a support material in printers with a dual or multiple extruders, in order to provide structure to an object with complex form. PVA is water soluble and is ideal for base support material in some complex designs. Parts with moving features and lots of overhangs, such a building models, are possible because the supporting structure can be easily removed after printing to deliver a finished look.
PROS:
- Recyclable
- Bio-grade
- Nontoxic
- Dissolvable in water
CONS:
- Special storage required, because of air moisture
- Hard to 3D print with
Polycarbonate (PC)
Polycarbonate is one of the strongest materials for FDM 3D printing at the moment. The material in general is used in number of industries like medical, food, automotive, aeronautics etc. It’s one of the most used thermoplastics for engineering purposes now days. Another upside is that PC is biocompatible and can be sterilized. Lastly 3D Printed parts with PC are strong, durable, accurate, with great mechanical properties and heat resistant.
PROS:
- strong and durable
- stiff and rigid
- great mechanical properties
- biocompatible
CONS:
- high printing temperature (about 300ºC)
- expensive compared to other materials
- tend to warp a lot
- requires a heating chamber
618 Nylon
This material is recommended to experience users. It can be challenging to 3D Printing Print with, due to the warping and bed adherence. 618 Nylon is stronger than ABS and PLA, and more chemically resistant with lower coefficient of friction. 3D printed parts offer flexibility and strength.
645 Nylon
3D Printed parts are strong still flexible. Suited for general industrial grade parts. Not easy to 3D print with due to warping and platform adhesion. 645 doesn’t emit any fumes when printed. Nylon 645 has the highest chemical resistance of all Nylons for 3D printing and is highly compatible where Nylon 6,6 is required!
680 Nylon
The 680 Nylon is pure polymer and it is FDA approved. This 3D Printing filament is great for clinical, food and medical industries. The filament itself is still not certified for those uses but it is in the process of! Testing is performed in compliance with US FDA manufacturing practice (GMP) regulations 21 CFR Parts, 210,211 and 820.
Why Choose 3D Printing with Nylon?
- When you need to make a print with extreme strength, durability and flexibility
- For end-use prototype that needs to be used and abused a lot, to test for optimal design
- For a replacement part that would coast a lot to buy otherwise
- Nylon offers a large variety of uses and has the most versatile list of properties
- You can dye nylon with interesting results. You can add variety of color effects, just make sure to dry your filament very well before use
- Suited for industrial grade parts
- High chemical resistance
- Lower coefficient of friction compared to other 3DP materials
- Not easy to 3D Print with
- Water up-take from local humidity
Last updated: 4/28/2017
ABS | PLA | PVA | HIPS | |
---|---|---|---|---|
Produced From | Petroleum | Plant starch | Petroleum | Petroleum |
Ecologically friendly | No | Yes | No | No |
Nozzle temperature | 210-250°C | 170-220°C | 190-220°C | 220-250°C |
Bed temperature | 80-120°C | 50-60°C | 50°C | 80-120°C |
Heated bed | Required | Not required/Beneficial | Not required | Required |
Print surface | PEI tape, PET tape, Kapton take | Blue tape/ PEI tape, PET tape, Kapton take | Blue tape/ PEI tape, PET tape, Kapton take | PEI tape, PET tape, Kapton take |
Additional cooling | Not required/Beneficial | Required | Not required | Not required/Beneficial |
Smell during printing | Smells bad /strong | Smells sweet | Smells slightly | Smells bad /strong |
Solubility | Acetone | Hot benzene | Water | (R)-(+)-Limonene |
Great for | Mechanical parts | High definition parts | Support material for PLA | Mechanical parts Support material for ABS |
Recycling | Code #9 | Code #7 | N/A | N/A |
Properties | Durable Strong Slightly flexible Heat resistant | Tough Strong | Water soluble Great film formation High bonding power | Durable Strong Slightly flexible Heat resistant Less warping than ABS |
Post-processing | Easy sanding Easy gluing Easy drilling Easy dissolvable in Acetone | Sanding possible Limited gluing | Dissolvable in water | Easy sanding Easy gluing Easy drilling Easy dissolvable in (R)-(+)-Limonene |
Pros | Excellent plastic properties Durable and difficult to break Excellent for mechanical parts Heat resistant | Bio-plastic Good smell Nontoxic No heated bed required High print speed Less wrapping and shrinking Excellent for small high-resolution parts Hard or flexible variants Easy to paint | Recyclable Bio-grade Nontoxic Dissolvable in water | Excellent plastic properties Durable and difficult to break Excellent for mechanical parts Heat resistant |
Cons | Heated bed required Smelly | Slow cooling down Low heat resistance Easier to break Limited post processing | Special storage required, because of air moisture | Heated bed required Slightly smelly |
First of all I would like to say fantastic blog!
I had a quick question in which I’d like to ask if you don’t mind.
I was curious to know how you center yourself and clear your thoughts before writing.
I have had difficulty clearing my mind in getting my ideas out there.
I truly do enjoy writing but it just seems like the first 10 to 15 minutes are lost simply
just trying to figure out how to begin. Any recommendations or hints?
Kudos!